What does Friction Facts’ Jason Smith bring to Ceramic Speed?
Jason Smith creates the data and components to make you cycle faster. Trizone caught up with the engineer from Friction Facts, now part of CeramicSpeed, who tests every minuscule part of a drive train, to uncover his remarkable role. Jason Smith is passionate about decreasing the friction losses on
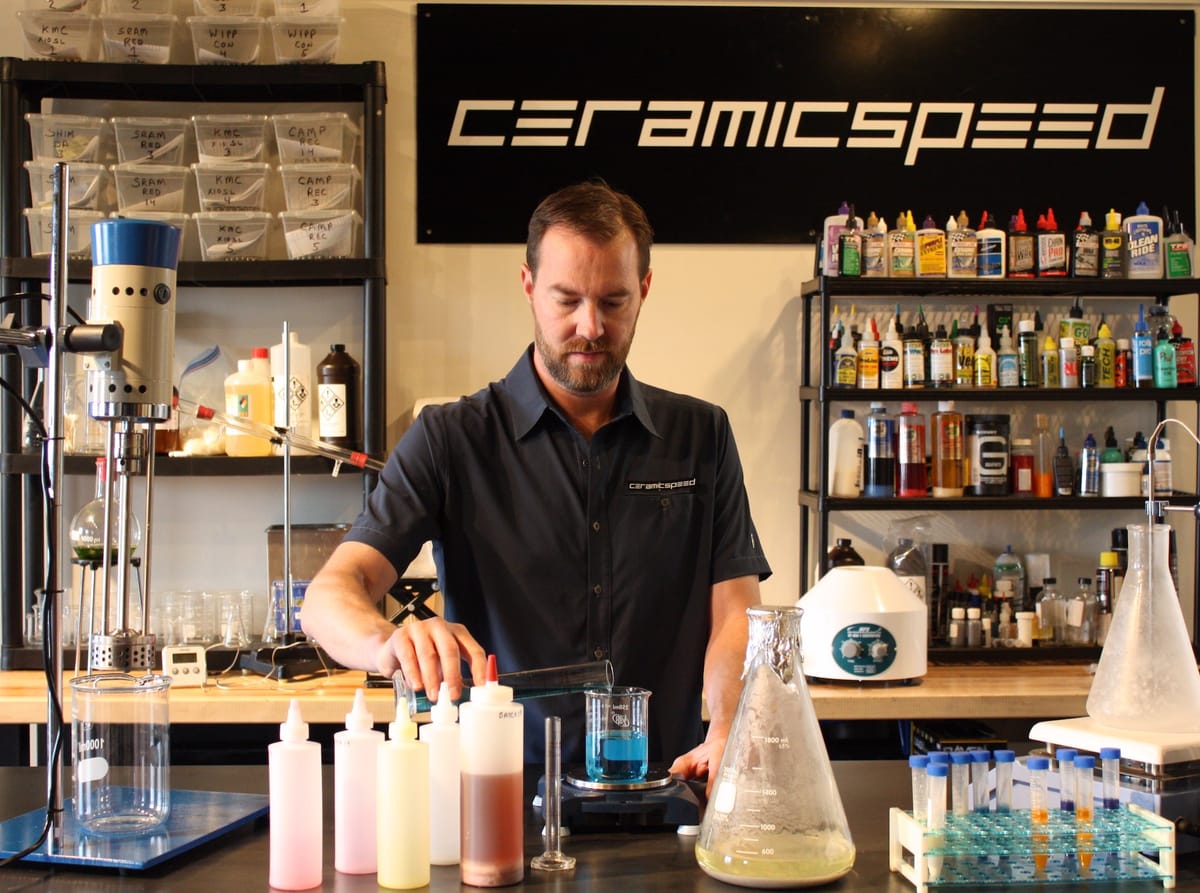
Jason Smith creates the data and components to make you cycle faster. Trizone caught up with the engineer from Friction Facts, now part of CeramicSpeed, who tests every minuscule part of a drive train, to uncover his remarkable role.
Jason Smith is passionate about decreasing the friction losses on your bike. He genuinely proves which products and habits can bring down your wasted watts to boost your speed through rigorous testing. “So many other companies say they have the fastest lube or product, but they don’t actually test! I’ve been testing products for four years,” says Smith brightly.
The journey began at Friction Facts
Jason Smith was recently snapped up by world-class bearing and bicycle components manufacturer CeramicSpeed. The new appointment began organically, thanks to the state-of-the-art testing equipment he personally invented for his own unbiased website Friction Facts. “Friction Facts was simply an independent testing lab,” he notes. “We’ve tested shift points, big ring vs. small rings, chain wear and its effects on friction and lubricants, and even techniques and practices riders can change to generate less friction. Now that CeramicSpeed has bought Friction Facts, my role will be focused more on product development, yet CeramicSpeed will continue to use the Friction Facts lab for unbiased tests.”
CeramicSpeed will offer the cycling industry the opportunity to use the Friction Facts lab to test any products that don’t create a conflict of interest. “For example, we can test a 1x vs. a 2x drivetrain,” says Smith. “CeramicSpeed doesn’t manufacture full drivetrains, so there’s no conflict of interest. But it’s definitely an area of interest for cyclists from an efficiency standpoint, and [we’ll] investigate it.”
CeramicSpeed invites Smith to R&D
Smith’s new role at CeramicSpeed has a uniquely organic origin. “Martin Banke, the Managing Director of CeramicSpeed, was actually my first customer at Friction Facts,” he says. “He contacted me to do some prototype testing for them. Since I knew the company it made sense for me to join their team as part of this acquisition.”

In his new role, Smith is now CTO and part of the CeramicSpeed R&D team. “I’m responsible for new products that haven’t come out yet in the lubrication world and new products that will optimize the drive train efficiency,” he says. Smith works hand-in-hand with another team of seven incredible scientists at CeramicSpeed’s R&D lab in Denmark. “Ph. D. in Chemistry Lina heads up the lubrication team there [in Denmark],” he adds. “Both the Product and Lubrication R&D teams are amazing. They’re so technology focused. In order for them to say they’re the world’s fastest, they have to prove it.”
Smith is thrilled to be working with such a passionate company. “CeramicSpeed has proven over the years they’re not just bearings; they can do so much. They’re very driven to develop new products that optimize performance.”
The dream of a frictionless drive train
The goal is to have a drivetrain with an absolute minimum of friction. “This is what we aim for,” Smith says eagerly. “But every little component of a bearing and the chain that we can improve to make the drivetrain a little bit faster all adds up.”
Smith blends his passion for testing with innovation at CeramicSpeed. “I’ve been testing products and techniques for so many years and getting ideas,” he says. “I’m hoping I can put a lot of my ideas into realistic, usable products for CeramicSpeed. And we have some pretty crazy ideas!”
Smith invents his own testing equipment… literally
Far from just another employee, Smith has invented the key testing elements CeramicSpeed now uses. “I invented quite a few of the equipment we use here,” he adds. “The equipment that I have created is all developed from scratch with a prototype, then made sure it worked and was repeatable.”
For those of us who don’t spend our days in a drive train testing lab, here’s a quick run down of the one-of-a-kind equipment available at the CeramicSpeed test facilities:
“A high precision chain tester. We use it to test chains, cross chaining, derailleurs, OSPW Systems and lube. It’s accurate to within 1/50th of a watt.”
“We built a pulley wheel bearing tester. It tests individual pulley wheels not in a system. [unlike most other testers who don’t isolate just one pulley wheel] We look at the bearing of a pulley wheel and this tester is accurate to 1/1000th of a watt.
“We have hub bearing and bottom bracket testers. We test multiple styles of bearings with an accuracy of 1/50th of a watt.”
“We have environmental machines where we can throw mud and crud at components and see how they react.”
If you’re reeling from all this technical information, all you need to know is Jason Smith is a genius, and he’s invented testing equipment no one else has even thought of. “We have precision equipment that does not exist anywhere else in the world,” he adds.
No, you don’t need to leave factory grease on a chain
Working in a testing lab, Jason Smith has become somewhat of a mythbuster. “There’s a huge misconception in the cycling world,” he notes. “There’s a lot of advice that says never remove the factory grease from a chain. People say once it’s gone, you’ll never be able to get lubricant down into the chain again. This just isn’t true!”
When Jason Smith makes a claim, he backs it up with tons of evidence. “There was never any data to support the efficiency of factory grease!” says Smith. “We’ve taken factory chains, tested them, stripped them, and applied efficient lubricant and it’s faster than the factory grease!”
Where did the myth about factory grease come from? “Any time an aftermarket liquid lube is applied to a modern ‘split bushing’ chain, it gets right down into the pins, bushings and rollers just fine,” he notes. “In the old days, the chains used solid bushings and weren’t designed to laterally flex so the lube couldn’t get down into the internals as easily, but that’s not the case anymore.”
Comments ()